Interested in Learning More?
Take control and choose the topics that interest you so we can make sure to only send you insights in those specific areas. Our professionals share timely business resources across a variety of industries. And don’t worry – you can update your preferences at any time.
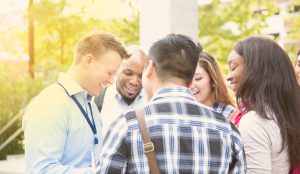
Meet the Team
Get to know the experienced tax, accounting and advisory professionals who are the catalysts for the growth and success of our clients. Purpose-driven, we help businesses be more profitable, efficient and productive in today’s fast-paced, tech-driven world.
Learn More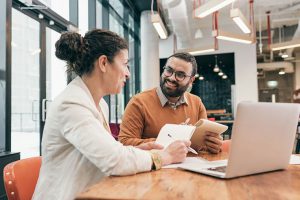
Experience the Culture
Values-driven with a commitment to advance inclusion and diversity in all aspects of our business, we live the Withum Way – 10 tenets that define the essence of Withum’s unique culture. We are #OneWithum.
Learn More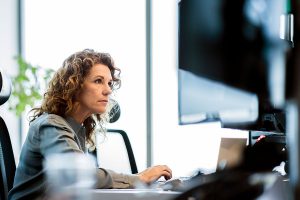
Industry
Our seasoned professionals possess the industry expertise across 14 different industry sectors supporting our clients. We offer insights and experience to keep you informed and to help you achieve your financial goals.
Learn More